Mighty Squirrel Brewery Steam Vent Odor Elimination
The Steam Vent Odor System (patent pending)
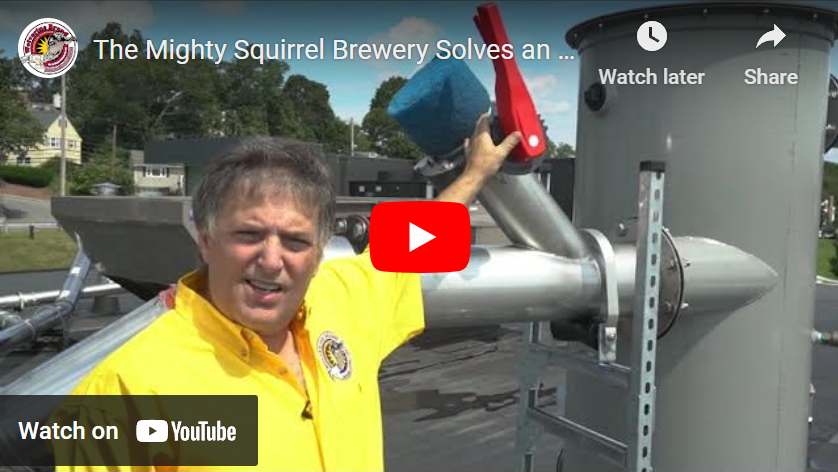
The Problem
The Mighty Squirrel Brewery in Waltham, Massachusetts is in a strip mall. The landlord asked Simple Solutions to control the odors that come from brewing beer, specifically, the odors coming from the kettle vents when the wort is boiling and the whirlpool vent when it is in operation. The landlords’ biggest complaint is the smell of rotting vegetables. The odors are noticeable up to ¼ mile away.
There is little information that can be found on eliminating the odors caused during beer brewing, but as home brewing and microbrew houses continue to expand in popularity the complaints of odors are easily found online. Industrial Odor Control’s first step was to gather information needed to design a system to solve the customers problem.
Next was to determine what the main compounds causing the unpleasant odors are during the boil and whirlpool stages of beer brewing and what we found was that there are two main compounds, hydrogen sulfide (H2S) and dimethyl sulfide (DMS). H2S has an odor like rotten eggs and DMS has an odor like that of rotting vegetables. DMS and H2S are mixed with steam and water vapors as it exits the kettle vent and the whirlpool vent. Though whirlpooling the wort does not boil the wort, the wort is put into the whirlpool once the boil is completed so its temperature is above the boiling temperature of both H2S and DMS during much of the process. Both elements have a boiling point of approximately 140° F.
The second step was to determine how many gallons per minute is exiting the kettle vent stacks during the boil process. It was found that the air stream is super saturated with water and both kettles combined lost .7 gallons per minute through the vent stacks in the form of steam.
Measuring the kettle vent stacks H2S and DMS concentrations, it was found that the H2S level at the kettle vents outlet was found to be between 15 PPM and 22.5 PPM depending on the stage of the boil. The DMS level was found to be more than 15 PPM at both the kettle vents and the whirlpool vent (15 PPM was the maximum concentration our Draeger tubes could read.) The whirlpool kettle vent was also found to have up to 22 PPM of H2S and more than 15 PPM of DMS while it was in use.
The biggest challenge was to design a system that can capture the exhaust from the kettles and whirlpool vent stacks, separate enough water so that the relative humidity is less than 99% so that the exhaust can be run through a vapor scrubber. This must be done without creating a vacuum in their vessels. Creating a vacuum will change the amount of water boiled out of the wort which will change their recipe and if the vacuum is large enough it can cause a vessel to collapse inward. Neither of these two scenarios is acceptable.
The Investigation
There is little information that can be found on eliminating the odors caused during beer brewing, but as home brewing and microbrew houses continue to expand in popularity the complaints of odors are easily found online. Industrial Odor Control’s first step was to gather information needed to design a system to solve the customers problem.
Next was to determine what the main compounds causing the unpleasant odors are during the boil and whirlpool stages of beer brewing and what we found was that there are two main compounds, hydrogen sulfide (H2S) and dimethyl sulfide (DMS). H2S has an odor like rotten eggs and DMS has an odor like that of rotting vegetables. DMS and H2S are mixed with steam and water vapors as it exits the kettle vent and the whirlpool vent. Though whirlpooling the wort does not boil the wort, the wort is put into the whirlpool once the boil is completed so its temperature is above the boiling temperature of both H2S and DMS during much of the process. Both elements have a boiling point of approximately 140° F.
The second step was to determine how many gallons per minute is exiting the kettle vent stacks during the boil process. It was found that the air stream is super saturated with water and both kettles combined lost .7 gallons per minute through the vent stacks in the form of steam.
Measuring the kettle vent stacks H2S and DMS concentrations, it was found that the H2S level at the kettle vents outlet was found to be between 15 PPM and 22.5 PPM depending on the stage of the boil. The DMS level was found to be more than 15 PPM at both the kettle vents and the whirlpool vent (15 PPM was the maximum concentration our Draeger tubes could read.) The whirlpool kettle vent was also found to have up to 22 PPM of H2S and more than 15 PPM of DMS while it was in use.
The biggest challenge was to design a system that can capture the exhaust from the kettles and whirlpool vent stacks, separate enough water so that the relative humidity is less than 99% so that the exhaust can be run through a vapor scrubber. This must be done without creating a vacuum in their vessels. Creating a vacuum will change the amount of water boiled out of the wort which will change their recipe and if the vacuum is large enough it can cause a vessel to collapse inward. Neither of these two scenarios is acceptable.
The Solution
An overhead image showing steam kettle odor solutionIndustrial Odor Control developed a unique vapor scrubber system that required the design of an air admittance tee (patent pending) and an air admittance lateral (patent pending). Both components were integral in achieving the goal of this project. The steam vent extraction and odor control system uses a pressure blower to move the air through the system. The size of the blower will vary depending on the brewery it is used on.
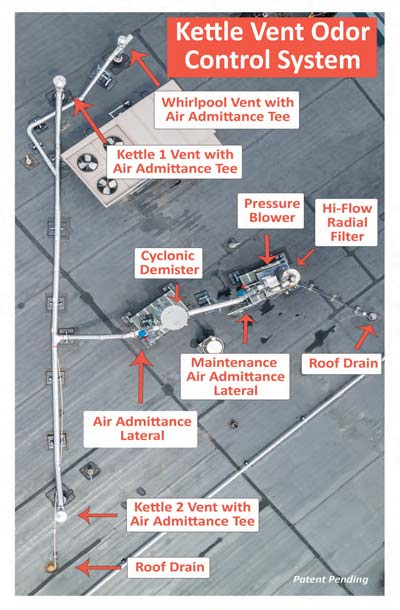
The steam vent odor control system utilizes an air admittance tee on top of each vent stack. The air admittance tee is where the exhaust from the kettle and whirlpool stacks is captured, and outside air is introduced to begin the process lowering the exhaust stream temperature down below the dew point. The dew point is where water vapors can condense allowing the water to be separated from the air stream.
The exhaust stream is then brought through our patent pending air admittance lateral where once again outside air can be metered into the stream prior to it entering a cyclonic demister. The cyclonic demister will separate any water that has dropped out of gas phase by getting the exhaust streams temperature below the dew point. The water that has been removed from the exhaust stream is captured and piped to a drain for safe disposal. The exhaust stream leaving the demister was measured at 94% RH, well below the point needed to run it through our vapor scrubber.
The exhaust streams next stop is another air admittance lateral, a pressure blower and then a high flow radial scrubber filled with a blended media tailored specifically for high RH air streams of H2S and DMS.
If the media has become saturated the air admittance tee located in front of the pressure blower is used to bypass the rest of the system and bring 100% outside air to the vessel which will rapidly purge the water from the filter.
The Results
Measuring the outlet stream of the radial scrubber for H2S and DMS it was found that there is 0 PPM H2S and 0 PPM DMS during the boil and whirlpool stage of the beer brewing process.
Download a Printable Copy of this Case Study.